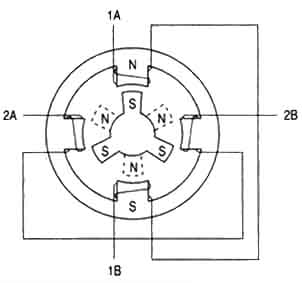 above (Diagram 1): Figure illustrating the
position of the six-pole rotor and four-pole stator of a typical stepper
motor. |
Stepper motor were designed on the principles of
electromagnetic theory in order to to make a motor turn a precise
distance when a pulse of electric current is applied. Recall from
basic physics that like poles repel and unlike poles attract. Diagram
1 (left) shows a typical cross-section a stepper motor's rotor and stator. Note that the stator (stationary winding) has four poles, and the rotor has six poles (three complete magnets).
The rotor will require 12 pulses of electricity to move the 12
steps to make one complete revolution. In other words, the rotor
will move exactly 30° for each pulse of electricity that the motor
receives. The number of degrees the rotor will turn when a pulse
of electricity is delivered to the motor can be calculated by dividing
the number of degrees in one revolution of the shaft (360°) by the
number of poles (north and south) in the rotor. In this stepper
motor 360° is divided by 12 to get 30°. |
When no power is applied to the motor, residual magnetism in the rotor
magnets will cause the rotor to detent or align one set of its magnetic
poles with the magnetic poles of one of the stator magnets. Hence, the
rotor has 12 possible detent positions. When the rotor is in a detent,
it will have enough magnetic force to keep the shaft from moving to the
next position. If you rotate the rotor by hand (with no power applied),
the effect just noted makes the rotor feel like it's clicking from one
position to the next .
When power is applied, it's directed to only one of the stator pairs
of windings, which will cause that winding pair to become magnetized.
One of the coils for the pair will become the north pole; the other will
become the south pole. When this happens, the stator coil which is the
north pole will attract the closest rotor tooth that has the opposite
polarity, and the stator coil which is the south pole will attract the
closest rotor tooth that has the opposite polarity. When current is flowing
through these poles, the rotor will now have a much stronger attraction
to the stator winding, and the increased torque is called holding torque.
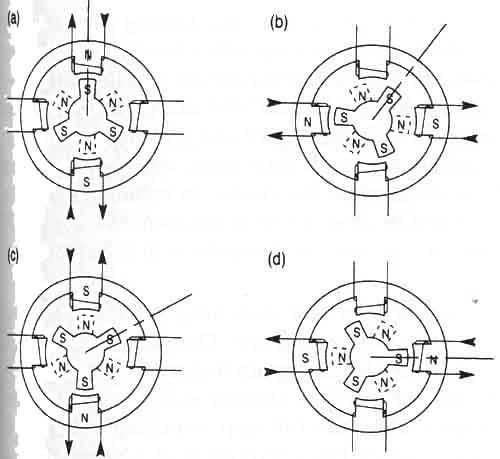
above (Diagram 2): Movement of a stepper
motor rotor as current is pulsed to the stator. |
Changing the current flow to the next
stator winding, the magnetic field will be changed 90°. The rotor
will only move 30° before its magnetic fields will again align with
the change in the stator field. The magnetic field in the stator
is continually changed as the rotor moves through the 12 steps to
move a total of 360°. Diagram 2 (left) illustrates the position
of the rotor changing as the current supplied to the stator changes.
In Diagram 2a (left) one can notice that when current is applied
to the top and bottom stator windings, they will become magnetized
with the top part of the winding being the north pole, and the bottom
part of the winding being the south pole. Note that this will cause
the rotor to move a small amount so that one of its south poles
is aligned with the north stator pole (at the top), and the opposite
end of the rotor pole, which is the north pole, will align with
the south pole of the stator (at the bottom). A line is placed on
the south-pole piece that's located at the 12 o'clock position
in Diagram 2a so that one can follow its movement as current is
moved from one stator winding to the next. In Diagram 2b current
has been turned off to the top and bottom windings, and current
is now applied to the stator windings shown at the right and left
sides of the motor. When this happens, the stator winding at the
3 o'clock position will have the polarity for the south pole of
the stator magnet, and the winding at the 9 o'clock position will
have the north-pole polarity. In this condition, the next rotor
pole that will be able to align with the stator magnets is the next
pole in the clockwise position to the previous pole, meaning that
the rotor will only need to rotate 30° in the clockwise position
for this set of poles to align itself so that it attracts the stator
poles.
In Diagram 2c notice that the top and bottom stator windings are
again energized, but this time the top winding is the south pole
of the magnetic field and the bottom winding is the north pole.
This change in magnetic field will cause the rotor to again move
30° in the clockwise position until its poles will align with the
top and bottom stator poles. One can see that the original rotor
pole that was at the 12 o'clock position when the motor first started
has now moved three steps in the clockwise position.
In Diagram 2d one can notice that the two side stator windings
are again energized, but this time the winding at the 3 o'clock
position is the north pole. This change in polarity will cause the
rotor to move another 30° in the clockwise direction. Note that
the rotor has moved four steps of 30° each, which means the rotor
has moved a total of 120° from its original position. This may be
verified by the position of the rotor pole that has the line on
it, which is now pointing at the stator winding that's located
in the 3 o'clock position.
|
HOME |
PREVIOUS: Stepper
Motors: Types | NEXT:
Switching
Sequence for Full and Half-Step Motors |