Observe the requirement outlined above for disconnecting means, controller, and overload units. Use wire with an ampacity of at least 125 percent of
the full-load current of the motor. For long circuits use wire larger than
required by NEC in order to avoid excessive voltage drop. If the circuit
to the motor is long, and you use wire that's too small, you may have
only 100 volts at the motor during the starting period instead of nearly
120 volts. The motor may not start, or if it does it will deliver significantly
less than its rated horsepower. The Table below shows the wire size to
use at various distances from service equipment to motor, assuming the
wire has an ampacity of at least 125 percent of the full-load current shown
on the nameplate of the motor. All distances are one-way. The table is
for single-phase motors only.
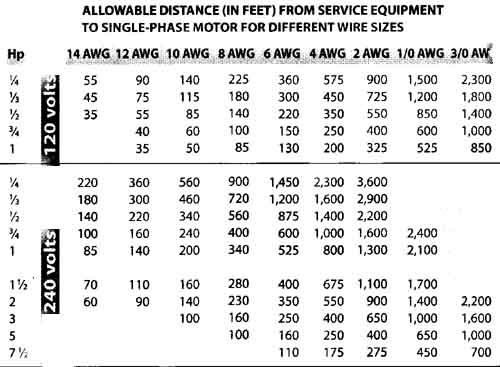
Table above: The wires shown in the table are compromises. The
voltage drop while starting (when the amperage is several times greater
than when the motor is running) will be from 3 to 7 1/2 percent depending
on the type of motor, how hard the load is to start, and other factors.
While running, the drop will be about 1 1/2 percent. This is less than
normally recommended for non-motor loads and is the result of wire sizes
large enough to keep the drop within reasonable limits while starting.
|