Separate circuits are recommended for individual motors that are not part
of an appliance if they are of more than 1/2 hp, whether directly connected
or belt driven. Use NEC Table 430.148, to determine the motor’s amperage.
Every motor must have a disconnecting means, a controller to start and
stop it, short-circuit and ground-fault protection, and motor overload
protection in case of overload or failure to start. Several of these are
often combined.
Disconnecting means
Every motor must have at least one disconnecting means capable of completely
isolating the motor from all ungrounded conductors so it can be maintained
safely. The NEC rules on motor disconnecting means fall into two categories.
First, the disconnecting means must be suitable to handle this duty, and
second, it must be located where those who may need to operate it will
be able to do so promptly. That concept is more fully explained under the
heading “In sight from requirements” below. Acceptable motor disconnecting
means generally used on projects within the scope of this book include
the following devices:
Motor-circuit switch—A switch, rated in horsepower, capable of
interrupting the maximum operating current of a motor of the same horsepower
rating as the switch at the rated voltage. The device must be listed to
qualify.
Circuit breaker—The circuit breaker in the panel-board, or separately
mounted, qualifies.
Molded case switch—A nonautomatic circuit breaker. Molded case
switches contain the switching mechanism and manual-operable handle of
circuit breakers, but no thermal or magnetic sensing mechanism that would
cause an automatic trip.
Manual motor controller additionally marked SUITABLE AS MOTOR
DISCONNECT—the diagram below shows some manual motor controllers. Even
though they are controlled manually and have OFF and ON positions, they
don’t qualify as disconnecting means without meeting additional qualifications
because they differ in robustness of construction from motor circuit switches.
The NEC allows them in two circum stances. The first, covering small motors,
allows them to be used as disconnects for motors of 2 hp or less, just
as snap switches (described later in this list). The second, covering larger
motors, allows them to be used as disconnects if they are on the load side
of the final branch-circuit short-circuit and ground-fault protective device.
In either case, their horsepower rating must not be less than the motor.
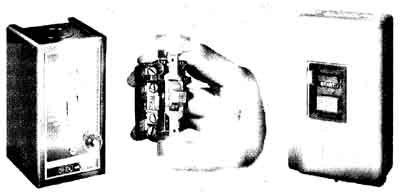
Above Diag. Controls of these types are “manual motor controllers.”
They are used to start and stop a motor; they also contain motor overload
devices. If marked SUITABLE AS MOTOR DISCONNECT they can additionally function
as the required disconnecting means. (Square D company).
General-use switch—A switch intended for use in general distribution
and branch circuits. It’s rated in amperes, and is capable of interrupting
its rated current at its rated voltage. See Diag. below for an example.
Its ampere rating must be not less than twice the full-load current rating
of the motor. It generally cannot be used for a motor larger than 2 hp,
unless it additionally qualifies as a motor-circuit switch, as described
earlier. Use a switch with one fuse for a 120-volt motor, and two fuses
for a 240-volt motor.
General-use snap switch—A form of general-use switch constructed
so that it can be installed in flush device boxes or on outlet box covers,
or otherwise used in conjunction with wiring systems recognized by the
NEC. (In other words, these are the ordinary switches used in controlling
lights in ordinary house wiring.) They are for ac motors only. To qualify,
the switch must be rated ac-only (general-use ac-dc snap switches are not
acceptable) and the motor full- load current must not exceed 80% of the
ampere rating of the switch.
Plug and receptacle—If the motor is portable, the plug on the
cord is sufficient if the motor rating does not exceed the horsepower ratings
that the test labs assume for the plug configuration. For example, a 125-volt,
15-amp receptacle can be used with up to a 1/2-hp motor, and a 125-volt,
20-amp receptacle is good for 1 hp; a 250-volt, 15-amp receptacle works
for up to 1 1/2 hp, and the 20-amp variety works for up to 2 hp.
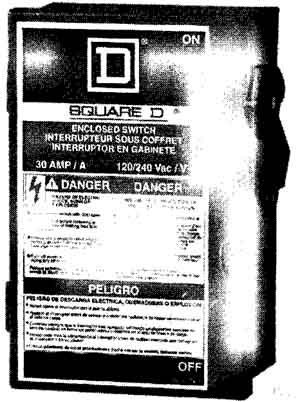
Above Diag. A switch of this type, or a larger one with cartridge
fuses, may be used with small motors. If the switch has two fuses, it’s
for a motor operated at 240 volts; if it has only one fuse, it’s for a
motor operated at 120 volts. (Square D company).
Controllers
A controller is any device used to start and stop a motor. It’s part of
the machine on refrigerators, pumps, and other equipment with automatically
started motors. On manually started motors it can be a circuit breaker
or switch, but is usually what is called a motor starter, as shown above.
The enclosure for the starter also contains motor overload devices, which
are discussed under the next heading. Controllers for motors over 2 hp
must have a horsepower rating equal to or more than the horsepower rating
of the motor. Use the smaller starter in the illustration for fractional-horsepower
motors; it has a manual switch to start and stop the motor. For bigger
motors, use the larger starter shown at the right. It has pushbuttons to
start and stop the motor. Larger starters have pushbuttons in a separate
case arranged to actuate a magnetic switch (usually called a “contactor”),
allowing the motor to be electrically controlled from a distance and from
multiple locations or by automatic means, such as through a pressure switch.
Motor overload devices
Motors must be protected by overload devices to prevent burnout and risk
of fire resulting from extended overload.
It takes many more amperes to start a motor than to keep it running at
full speed at its rated horsepower. And when a motor is overloaded, it
consumes more amperes than while delivering its rated horsepower. A motor
won’t be damaged by current considerably larger than normal flowing through
it for a short time, as at start-up or during a momentary overload. But
it will burn out if more than normal current flows through it for a considerable
time.
A motor overload device permits the high starting current to flow for
a short time, but disconnects the motor if current due to overload (or
failure to start) flows through it for a considerable time. Overload devices
are permitted to be separate, but in practice they are usually included
in the same enclosure with the starter.
Overload devices include “heaters” and are rated in amperes. When the
starter is installed, select an overload device heater on the basis of
the full-load ampere rating on the nameplate of the motor. Overload devices
are often integral with (built into) the motor in the case of small motors,
also with many larger motors if they are part of automatically started
equipment such as air-conditioning units. Whether integral or separate,
if the overload device stops the motor, correct the condition that led
to the overload. Let the motor and the overload device cool off, then reset
manually.
Some overload devices are automatically resetting, but they must not be
used where the unexpected restarting of the motor (For example when powering
a table saw) could result in injury.
Motor branch-circuit short-circuit and ground-fault protection
Motor overload devices, whether built into the motor or installed on the
starter, are not capable of interrupting the high amperage that can arise
instantaneously in case of a short circuit or ground fault that might occur
in the motor circuit or in the motor. The branch circuit as well as the
controller and the motor must be protected by fuses or circuit breakers
against such shorts or ground faults.
The wires in a motor branch circuit must have an ampacity of at least
125 percent of the full-load motor current so they won’t be damaged if
the motor is overloaded. (Overload devices permit up to about 25 percent
overload current for a consider able time before stopping the motor.) For
motors of the kind typically installed in homes and on farms, the NEC permits
a breaker to have an ampere rating up to 250 percent of the full-load current
of the motor; if time-delay fuses are used, their ampere rating must not
exceed 175 percent of the full-load current. If these values seem to contradict
the basic requirement that overcurrent devices may not have an ampere rating
larger than the ampacity of the wire being protected, bear in mind that
a motor circuit is a special case in which the overcurrent device protects
only against short circuits or grounds. Protection against lower values
of overcurrent (overload, or failure to start) is provided by the motor
overload device discussed under the previous heading. Use the smallest
rating that will permit the motor to start and operate properly. Fuses
that are not of the time-delay type should not be used.
“In sight from” requirements
A motor disconnecting means must be in sight from the motor controller;
there are no exceptions that normally apply to this rule. In addition there
must be a disconnect in sight from the motor and its driven machinery.
The NEC defines “in sight from” as being visible and not over 50 feet from
the specified location. If you notice one component from the other but
they are more than 50 feet apart, they are not “in sight from” each other.
This concept, which originated in the NEC motor article, is now formally
defined in NEC Article 100 for use throughout the NEC.
If the controller disconnect is not in sight from the motor and its driven
machinery you must install an additional disconnecting means that is in
sight from the motor and its driven machinery. This additional disconnecting
means must meet the requirements for the disconnecting means already discussed,
but if it’s a switch it need not have fuses. There is an exception that
allows the in-sight disconnect to be omitted if the disconnecting means
for the controller can be individually locked in the open position; however,
effective with the 2002 NEC that exception is now limited to installations
where the additional disconnect would introduce additional hazards or would
be impracticable. For example, it would be plainly impracticable to place
a disconnect 50 feet down a well shaft to be “in sight” (not over 50 feet
distant) from a submersible pump motor 100 feet down the same shaft. |