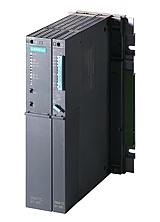
ABOVE: SIMATIC Controller from Siemens |
Although programmable
controllers have been available since the mid-1970s, developments-such
as the ready availability of local area networks (LANs) in the
industrial environment, standardized hardware interfaces for manufacturer
interchangeability, and computer software to allow specification
of the control process in both traditional (ladder logic) and more
modern notations such as that of finite-state machines-have made
them even more desirable for industrial process control.
Programmable
logic controllers are typically implemented by using commonly available
microprocessors combined with standard and custom interface boards
which provide level conversion, isolation, and signal conditioning
and amplification. Microprocessors used in programmable controllers
are similar or the same as those used in personal computers. The
software of a programmable controller must respond to interrupts
and be a real-time operating system, characteristics which the
typical operating system of a personal computer does not possess.
Perhaps the biggest benefit of programmable
controllers is their small size,
which allows computational power to be placed immediately adjacent
to the machinery to be controlled, as well as their durability,
which allows them to operate in harsh environments. This proximity
of programmable controllers to the equipment that they control
allows them to effect the sensing of the process and control of
the machinery through a reduced number of wires, which reduces
installation and maintenance costs. The proximity of programmable
controllers to processes also improves the quality of the sensor
data since it reduces line lengths, which can introduce noise and
affect sensor calibration. |